Internal inspection of an insulated tank
Some storage tanks are exposed to degradation that can weaken them and lead to accidents.
They must be regularly monitored to prevent these risks. Tanks that store products hazardous to people or the environment are subject to regulatory inspections, as outlined in the decrees of October 4th and 5th, 2010. This Industrial Facilities Modernization Plan (PM2I) includes inventory, initial condition assessment, and the required inspection plan.
Insulated tanks are more complex to inspect, as the areas of interest are located beneath the insulation, out of the inspector’s direct reach.
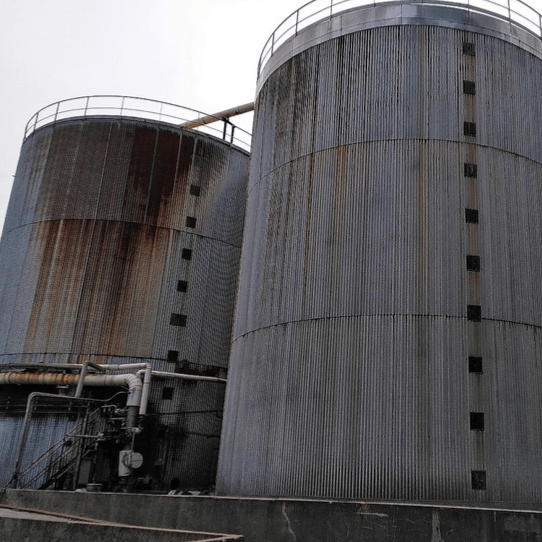
Client challenges
Insulation can lead to water retention through runoff or condensation, which promotes localized corrosion. These areas are difficult to monitor because they are out of reach for inspectors.
To limit costs, industrial operators and inspectors typically define a few measurement points called inspection wells where spot thickness measurements are taken.
However, these methods inherently involve work at height (scaffolding setup, aerial platforms, rope access), which can raise legal concerns such as the use of rope access technicians when less hazardous alternatives exist (Article R4323-64 of the French Labor Code). In terms of cost, scaffolding construction is almost always more expensive than the inspection itself.
Although these spot checks comply with the DT94 standard, they often lack representativeness something that cannot be compensated for by a simple visual inspection of the shell.
Solution
For these reasons, a maintenance manager at a paper mill consulted us. He wanted to carry out the internal inspection of an insulated tank measuring 11.5 meters in diameter and 14 meters in height, without using access equipment.
We have been developing robots and solutions for over 10 years to help operators avoid taking risks in their work environments.
For this client, we deployed the UT_Pole and Altiscan to perform continuous ultrasonic thickness measurements (B-scan).
The B-scan report provided the client with a clear profile of the tank’s shell thickness. Thousands of data points were summarized and ready to be used for calculation reports and to plan any necessary maintenance operations.
During this project, the internal surface of the shell showed heavy roughness and “layered” corrosion. We were able to test SONIC (a prototype for surface cleaning), which significantly improved the quality of our continuous thickness measurements on the shell.
Results
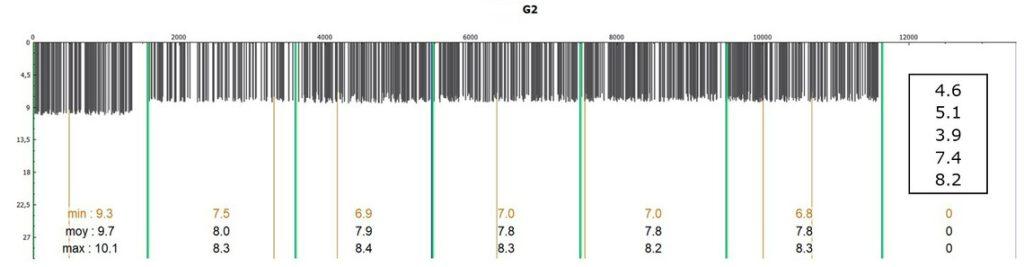
In conclusion, it took us just half a day on site to complete the inspection of the tank’s four vertical seams.
As a result, our client saved several hours of work, simplified the management of the intervention, and benefited from a much more detailed report thanks to the B-scan.