Non-Destructive Testing in Industry
Our History
Non-Destructive Testing in Industry
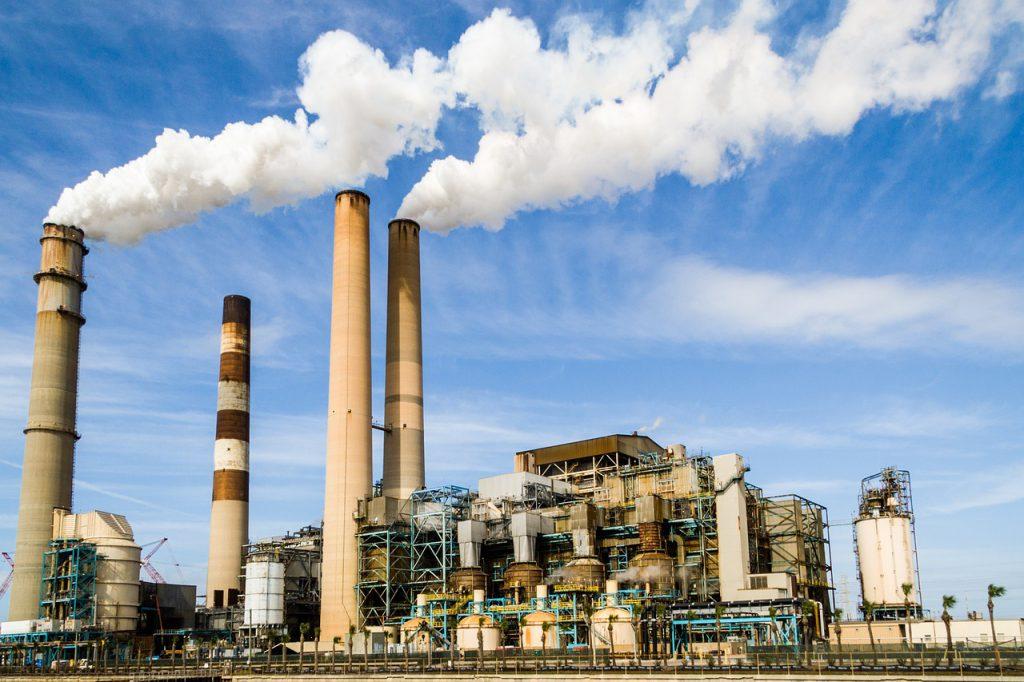
Every year, corrosion causes 25% of the world’s steel production to disappear.
At a global cost of approximately 3% of the world GDP.
The majority of industrial installations in OECD countries date back to the second half of the 20th century.
These include electricity generation, oil refining, chemicals, rail transport, cement production, steel, paper, sugar production, and broadly the entire secondary sector and maritime transport.
To prevent accidents, Non-Destructive Testing (NDT) is carried out.
Non-Destructive Testing (NDT) is a technique for evaluating the properties of materials.
These NDT techniques are implemented for the periodic inspection of storage tanks, spheres, vessels, columns, chimneys, electrofilters, filter bags, furnaces, boilers, pipelines, chutes, hoppers, ship hulls, and connected pipelines and tubing.
The goal of thickness measurements and visual inspections is to anticipate failures, such as loss of sealing and structural strength of equipment, which could pose risks to safety, health, the environment, and the performance and profitability of a site.
Among these risks, equipment failure in production can result in:
A risk of workplace accidents caused by a product leak, collapse, urgent and poorly prepared intervention,
A risk of environmental damage and pollution,
The need for emergency maintenance, which is more expensive and less efficient,
Production downtime, with ongoing production halted across the plant,
A loss of revenue due to reduced site operation rates, increased maintenance costs, and legal and reputational penalties in the event of human or environmental damage.
Prevent industrial risks through the implementation of Non-Destructive Testing (NDT)
The highest-risk installations are subject to regulatory inspections. These are equipment subject to specific regulations (pressure equipment, storage tanks, chimneys, etc.).
In France, regulatory inspections are carried out by Authorized Bodies (Bureau Véritas, Apave, Institut de Soudure, SGS, etc.).
These companies verify the compatibility of equipment with the relevant regulatory requirements.
In this context, they prescribe a series of Non-Destructive Testing (NDT) procedures, analyze their results, and produce strength calculations, aging assessments, and recommendations.
Industrials comply with these regulatory requirements by implementing an inspection schedule for their equipment, assigning qualified personnel to monitor this, and allocating dedicated budgets.
In addition to regulated equipment, a very significant portion of production equipment is exposed to the effects of corrosion, abrasion, and cracking.
These pieces of equipment do not follow a regulatory inspection plan, although they are essential to the site’s operation.
To check their integrity, these assets are generally inspected internally by maintenance technicians using basic NDT tools (single-element thickness gauges, vibration measurement equipment, etc.).
In the context of the aging of Western industrial installations, the risk of failure is increasing.
The proportion of inspections on unmonitored equipment is steadily rising.
Improve the accessibility of NDT
The labor code prohibits the use of rope access workers and requires the implementation of collective protective measures (PIRL, platforms, scaffolding) even at low heights. The total cost (direct costs, coactivity, access organization, specific risks, regulatory constraints) of these access means is higher than that of the inspections themselves.
The time required, costs, and regulatory constraints often make these inspections prohibitive.
Following the founding event of ROBOPLANET, the sinking of the ERIKA, a large number of industrial structures fail every year, resulting in human, ecological, and economic consequences for their environment.
Some interesting facts
Key figures to remember
« ROBOPLANET’s contribution is to offer NDT solutions that make inspections more accessible, expanding their use, and improving the safety and competitiveness of industrial sites. »