Inspection of suspect roofs
Usage and optimization plans for industrial structures drive operators to extend the lifespan of storage tanks as much as possible. As a result, some structures show signs of weakness, particularly the roofs, which can sometimes lead to fatal accidents for operators. Yet, technical solutions do exist.
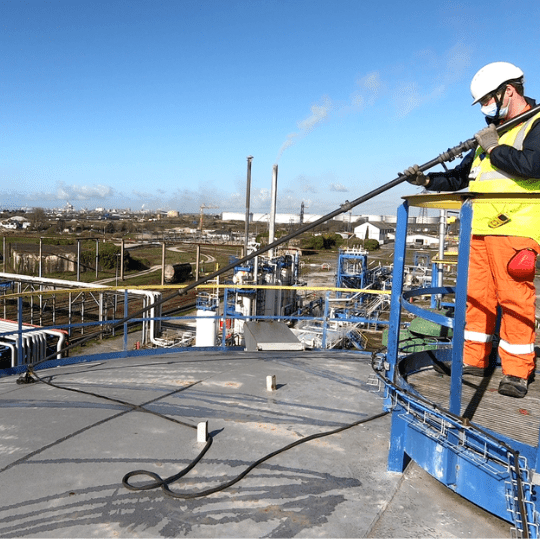
Client challenges
Even today, inspectors still go directly onto the roofs to perform spot ultrasonic thickness measurements. However, since these measurements are few in number, they often lack representativeness, which does not reassure the operator. Furthermore, spot measurements do not always provide visual data of the ultrasonic signal (A-scan), making it difficult to confidently validate the measurement point, especially when the area is degraded—which is often the case on storage tank roofs.
Moreover, the operator’s production departments struggle to free up certain production tanks for inspections or maintenance, resulting in only a few days of availability per year. The evolving HSE practices and regulations are pushing the operator to update their intervention techniques, especially after experiencing serious accidents or fatalities related to interventions on « weak » roofs.
SOLUTION
All these considerations lead our client, a petrochemical industrial operator, to consult us for the inspection of suspect tank roofs at their high SEVESO threshold site. In response, ROBOPLANET deployed UT_POLE—a telescopic boom that enables automated ultrasonic thickness measurements. Quick to install and with a deployment capacity of up to 12 meters, the operator remains within collective protection zones while carrying out inspections.
This operational approach is highly reassuring for both the operator and the management, who benefit from reduced HSE planning burdens and minimized intervention risks. UT_POLE performs continuous thickness measurements (B-scan, with at least one measurement per centimeter), providing a more reliable and representative assessment of the roof’s condition. This increases the likelihood of detecting localized corrosion.
Additionally, the B-scan report delivered provides the client with a clear profile of the tank roof’s thickness. Thousands of measurement points (at least one per centimeter) are summarized and ready for use by the maintenance team. During the inspection, another challenge arose: the degraded surface condition of some roofs. Foam present on the roof interferes with the ultrasonic wave’s propagation between the probe and the metal sheet, and high surface roughness further hampers both the inspection process and the quality of the results.
Other similar issues may be encountered, such as layered corrosion, roughness, or deposits like dirt, fungi, or dust. This is why we developed complementary equipment to prepare the surfaces in these areas, thereby enhancing the quality of the measurements.
RESULTS
in conclusion, it took us 2 hours on site to cover 4 spans of approximately 11 m each, with continuous measurements equivalent to 4,400 individual point measurements. As a result, our client received a much more detailed report of their roof, all under optimal safety conditions for the operator.